
Court clarifies the meaning of "reasonable practicability" in OHS after finding a Magistrate has misstated the test
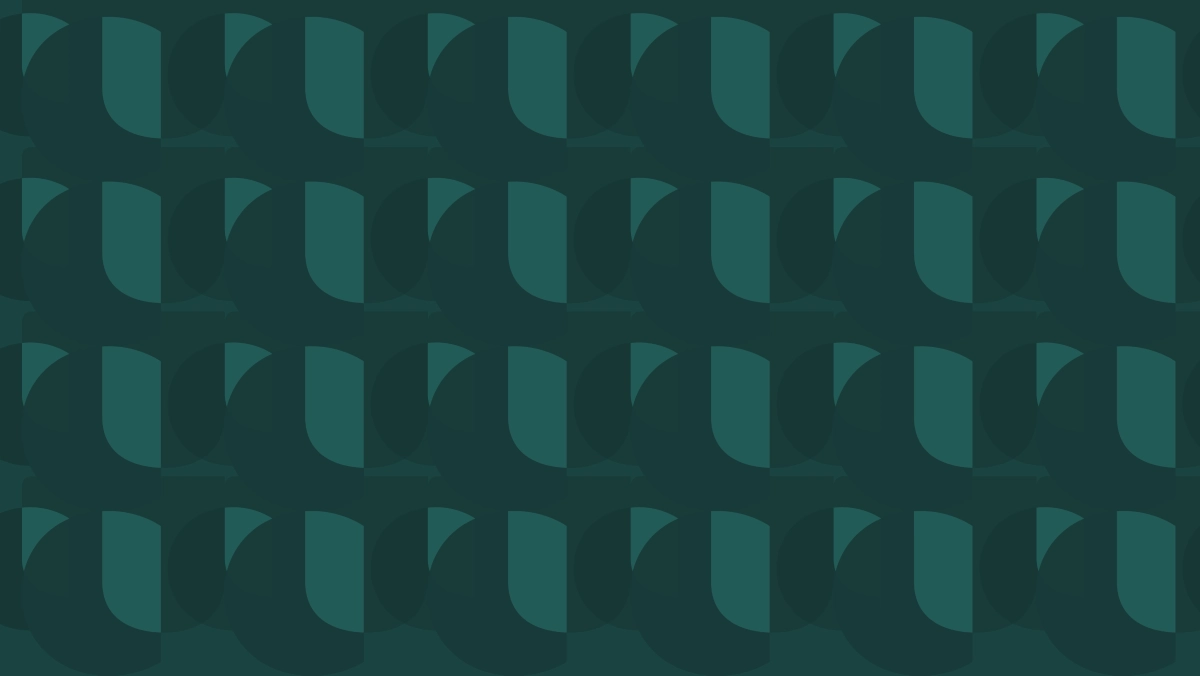
An employer has been successful in an appeal against its convictions on three charges under OHS laws, with the Victorian Supreme Court finding the Magistrate "impermissibly reasoned backward" and misstated the reasonable practicability test (SKM Services Pty Ltd v Magistrates' Court of Victoria & Anor [2019] VSC 460).
In the primary court, the Magistrate recorded convictions against the employer, imposed fines of $150,000 and ordered the employer to pay $45,000 of statutory costs after a worker received an amputation injury from a baling machine within the employer's recycling business. The employer was charged pursuant to section 21 of the Occupational Health and Safety Act 2004 (Vic) (OHS Act) in relation to failing to provide and maintain safe plant or a safe system of work for handling the bales.
The employer argued it took all reasonably practicable steps to ensure workers safety by ensuring the manufacturer of the machines had appropriate assessments and certificates in place before procuring the machines. It further contended that it was assured by the expert supplier that the baler had appropriate safety sensors and met guarding standards.
However, Magistrate Megan Aumair did not accept the employer's argument and held the employer could have taken further steps in order to reduce risks to its workers.
The appeal: "could" or "should"?
The employer appealed against its conviction, raising a number of arguments including that the Magistrate erred in relation to the test for reasonable practicability.
The elements of a section 21 offence are as follows:
- there was a risk to employee health and safety;
- the measures identified by the prosecution as necessary would have eliminated or reduced the risk (as the case may be); and
- it was "reasonably practicable" in the circumstances for the employer to have taken those measures.
The Court confirmed that the onus is on the prosecution to prove all elements of a charge for contravention of section 21, including the element of reasonable practicability of the measures that the prosecution says should have been taken.
In upholding the appeal, the Court found the Magistrate misstated the test for reasonable practicability by its finding that the employer "could" have foreseen the risks and implemented appropriate engineering controls accordingly, namely in the form of tunnel guarding on the aluminium and steel can balers.
Associate Justice Lansdowne further stated that the Magistrate's use of the word "could" rather than "should" in numerous parts of the Magistrate's judgment "supports an inference that the Magistrate impermissibly reasoned backward from what had happened, and how readily it could, in hindsight be guarded against, rather than examining the question on the basis of what [the employer] should have foreseen prior to the injury." It was this that led the Magistrate into error of applying the wrong test of reasonable practicability.
What is the correct application of the reasonable practicability test?
In determining what is (or was at a particular time) reasonably practicable in relation to ensuring health and safety, the OHS Act provides that regard must be had to the following matters:
- the likelihood of the hazard or risk concerned eventuating;
- the degree of harm that would result if the hazard or risk eventuated;
- what the person concerned knows, or ought reasonably to know, about the hazard or risk and any ways of eliminating or reducing the hazard or risk;
- the availability and suitability of ways to eliminate or reduce the hazard or risk;
- the cost of eliminating or reducing the hazard or risk.
The Court specifically considered the third element under section 20(2)(c) which refers to refers to actual or constructive knowledge.
The Court emphasised that section 20(2)(c) requires consideration on what the employer ought to have known about the risk and ways to eliminate or reduce it, as opposed to what it could have known. Additionally, the prosecution is required to establish what the employer should have done, as opposed to what it could have done. These matters must be considered at the time of the alleged contravention.
The Court noted that expert reliance (such as the employer's reliance on the assurances of the expert and skilled supplier) may be relevant to determining whether the employer's reliance on the assurances of the supplier was reasonably practicable as the employer's actual or constructive knowledge is a relevant factor.
While it was not dealt with by the parties in detail, the Court contemplated the question of why the employer should have foreseen a risk of injury and installed tunnel guards when it had been told by the supplier that they were not required.
Takeaways from this decision
This decision confirms that the Court must consider what the employer / persons conducting a business or undertaking (PCBUs) should have foreseen and done to manage risk having regard to, amongst other things, the actual or constructive knowledge of the employer / PCBU at the time of the contravention.
While employers / PCBUs will be guided by the assurances, information and testing results provided to them by the upstream duty holders with respect to plant (eg. designers, manufacturers, suppliers), particularly where the supplier has expert or specialist skills or knowledge, the employer / PCBU must still consider what other steps it should take having regard to what it knows or ought reasonably know about the risk.
We recommend the following practical steps to assist employers / PCBUs in discharging their duties with respect to plant and evidencing what they know, or ought reasonably know:
- undertake a documented due diligence process for the procurement of plant to satisfy yourself that:
- the plant is appropriate for the intended use, workplace and nature of work undertaken in the business; and
- the designer, manufacturer, supplier etc. of plant has the sufficient expertise and skill to provide safe plant,
- request information from the designer, manufacturer, supplier etc. regarding hazards, risk assessments, controls and the safe use, maintenance and storage of the plant;
- query whenever the information provided does not appear to be sufficient;
- keep records of all correspondence, information, testing results, documents or manuals provided by the designer, manufacturer, supplier etc.; and
- assess the safety of the plant and the system of work both once the plant is installed and on a regular basis thereafter (or engage a third party to do so particularly where the plant is specialist plant).
Get in touch
