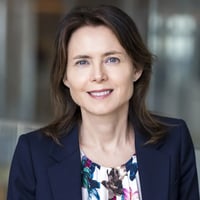
How Australia's building and construction sector is responding to the "hidden" issue of a building's embodied carbon
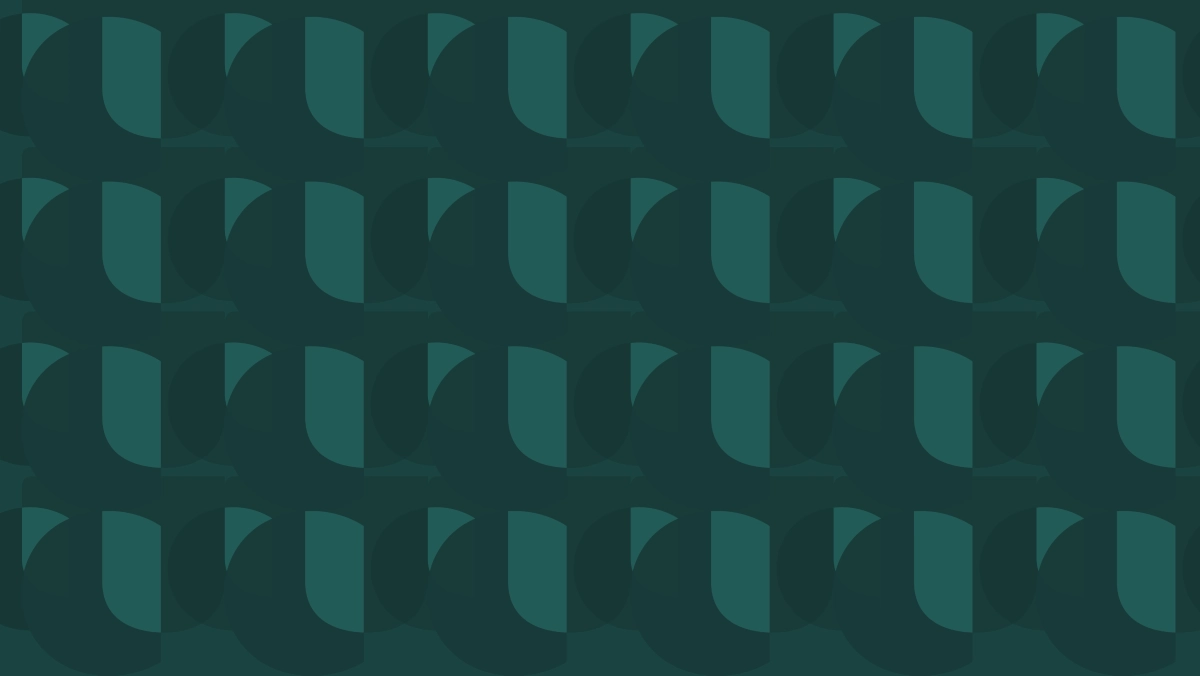
In the Federal Government's recent pledge to achieve net zero emissions by 2050, the Government recognised the importance of decarbonising Australian's building industry in achieving net zero. Indeed, modelling suggests that this industry must nearly entirely decarbonise by 2050 if Australia is to meet its goal.
Previously, when considering the carbon footprint of a building, the focus has been on its operational carbon – ie. the greenhouse gases emitted from all the energy sources used when the building is in operation. This includes the energy sources used to heat or cool a building, as well as ventilate and light it.
Attention, however, is now being paid to the concept of "embodied carbon" (also referred to as the "hidden impact" of a building). Simply put, embodied carbon can be understood as the sum of carbon (or greenhouse gases more generally) emitted in association with the construction of the building as well as the end of life stages of a building. (We note for the sake of completeness that some embodied carbon analysis focuses only on the "upfront carbon emissions" of the building construction phase and not those associated with maintenance and repairs or the end of life stage.)
However, it is generally accepted that embodied carbon comprises the greenhouse gas emissions associated with:
- the production and manufacturing of materials for the building;
- the construction of the building;
- maintenance, repairs and refurbishments during the building's life;
- the end-of-life stages of a building, including deconstruction / demolition, waste processing and disposal; and
- the transport of materials during the production, construction and end of life stages.
So, why is it a big issue?
According to the Property Council of Australia, embodied carbon accounts for approximately 11 per cent of carbon emissions worldwide. In Australia, 16 per cent of Australia's built environment emissions in 2019 comprised embodied carbon. As Australia increasingly decarbonises the electricity grid, embodied carbon – which is largely locked in by the time a building is constructed – will become a greater percentage of built environment emissions and a significant hindrance for the building and construction industry (and also Australia more generally) reaching net zero.
In July 2021 this year, the Green Building Council Australia (GBCA) and thinkstep-anz (with funding from the Commonwealth Government through the Department of Industry, Science and Energy Resources) published the report "Embodied Carbon & Embodied Energy in Australia's Buildings". This report calculated embodied carbon (and embodied energy) in Australia's commercial and residential buildings in a 2050 business-as-usual scenario against the 2019 baseline. According to the report, without intervention, embodied carbon will account for 85 per cent of Australia's built environment emissions in 2050 "at a time when Australia must achieve net zero emissions in line with the Paris Agreement".
According to the recent report "Taking Action on Embodied Carbon" by construction company Built, as a rule of thumb, superstructure and substructure account for the most upfront carbon emissions of a building, with concrete and steel typically making up the greatest proportion of a building's upfront carbon.
Embodied carbon: case studies
Several members of the building and construction sector in Australia are spearheading the construction and renovation of buildings with significantly reduced embodied carbon footprints.
The new Atlassian headquarters, located in Sydney to be completed in 2025, will be the tallest hybrid timber structure in the world and currently sets the benchmark for innovative, sustainable construction. The headquarters have a target of half the embodied carbon of a conventional building. The reduced embodied carbon footprint is being achieved using a hybridized structural system consisting of mass timber, concrete and steel.
Lendlease's International House Sydney and Daramu House have been similarly constructed using timbers. Specifically, International House Sydney uses cross laminated timber and glue laminated timber, with lower carbon footprints compared to other building materials. Zero waste is produced during the production process and the timbers are sourced from certified sustainably managed forests.
These development exemplify the different ways to reduce the embodied carbon of a building during the design and construction stages, which include (but are, of course, not limited to):
- substituting traditional emissions-intensive concrete with lower carbon varieties or the concept of net-zero concrete where any residual emissions are captured or offset;
- opting to use other materials like timber, exclusively or as much as possible, instead of concrete and steel;
- utilising existing infrastructure on the site and recycled content where practicable; and
- reducing the quantity of materials used.
What's on the horizon for embodied carbon
One of the main issues with embodied carbon is the difficulties with measuring it. As the GBCA and thinkstep-anz report notes "[t]here is an urgent need for additional policy incentives to decarbonise Australia’s energy supply and for investment in research and development of new materials and practices".
The National Australian Built Environment Rating System (NABERS), with funding from the NSW Government, is now investigating and developing a framework for measuring, benchmarking and certifying emissions from construction and building materials. It is envisioned that the framework will be incorporated into the current NABERS suite and commercial buildings and apartment blocks will begin to be rated on the amount of embodied carbon they contain.
In the future, constructing new sustainable buildings with low embodied carbon footprints will not be the entire solution. The building and construction industry will need to come up with innovative ways to renovate and reuse existing buildings and infrastructure with potentially high embodied carbon footprints and embrace the circular economy. This may require changes to legislation, particularly the heritage laws in the different states and territories, as well as clear financial incentives. NABERS has been hugely successful in increasing the energy and water efficiency of constructed buildings and it is likely that the market will demand a similar framework for rating embodied carbon for future developments.
Get in touch
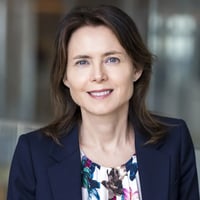